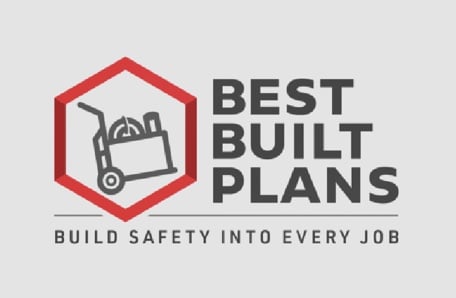
Contractor Planning Tool
Improve Productivity & Meet Schedules
Productivity drops and schedules get delayed when workers have to wait for materials to be delivered or spend time and energy locating and manually lifting and carrying materials around a jobsite. Industry stakeholders estimate that:
- The average daily waiting time by trade ranges from about 45 minutes to 83 minutes.(1)
- “Every 1 minute spent on pre-planning saves 6 minutes in the field.” (2)
Planning to reduce manual materials handling is a key part of Lean Construction and other approaches used to improve construction performance. Productivity can be improved when plans incorporate the following:
- Lifting equipment – The Ohio Bureau of Workers’ Compensation found a reduction in days lost due to soft tissue injuries (back injuries, etc.) when contractors used selected lift assist equipment. (3)
- Lift teams – Researchers found that two-mason lift teams reduced the risk for injury and reduced by 37% the average amount of time to build a wall. (4) Mason contractors that use two-mason lift teams cite benefits including safety (less wear and tear on workers, less low back stress, and less fatigue) and increased productivity.(5)
- Lower-weight materials – An industry study of light-weight block produced an average increase in production of 14.7%.(6)
- Prevention through Design (PtD) – Contractor and employee developed solutions, for example building a slide from plywood or lumber to move a material to a lower level where it will be used, can reduce manual materials handling.
- Storage – Construction materials delivered on pre-loaded and stackable carts reduce the risks of multiple unnecessary handling of material, and of potential soft tissue injuries.(7)
Sources:
1. Mastroianni, R. (2010). “A Contractor’s Perspective.” Lean Construction Institute, LCI Michigan Chapter – Kickoff Meeting, East Lansing, MI, May 6, 2010 (accessed October 2017)
2. Cramer, M.D. (2010). “Lean Construction at Dee Cramer.” Lean Construction Institute, LCI Michigan Chapter – Kickoff Meeting, East Lansing, MI, May 6, 2010 (accessed October 2017)
3. Ohio Bureau of Workers’ Compensation. “Ergonomics Best Practices for the Construction Industry.” (accessed October 2017)
4. Moraski, P., et.al. “Two-Mason Lift Technique” (video). Eastern Washington University.
5. Hess, J. et.al. (2010) “Ergonomic Best Practices in Masonry: Regional Differences, Benefits, Barriers, and Recommendations for Dissemination.” Journal of Occupational and Environmental Hygiene, 7: 8, 446-455, June, 1, 2010.
6. Lochonic L [2003]. Lightweight CMU: A weight off our shoulders. Livonia, MI: Masonry Institute of Michigan, The StoryPole, 34(4). [www.escsi.org]. Date accessed: December 2017. See ROI example based on this study: “CMU-Based on Unit of Material” at www.safecalc.org
7. 2016 AGC-Willis Towers Watson Construction Safety Excellence Awards Safety Management Showcase, Task Design – Engineering Controls & Design for Safety, p6.